Insulated Siding Installation Cost
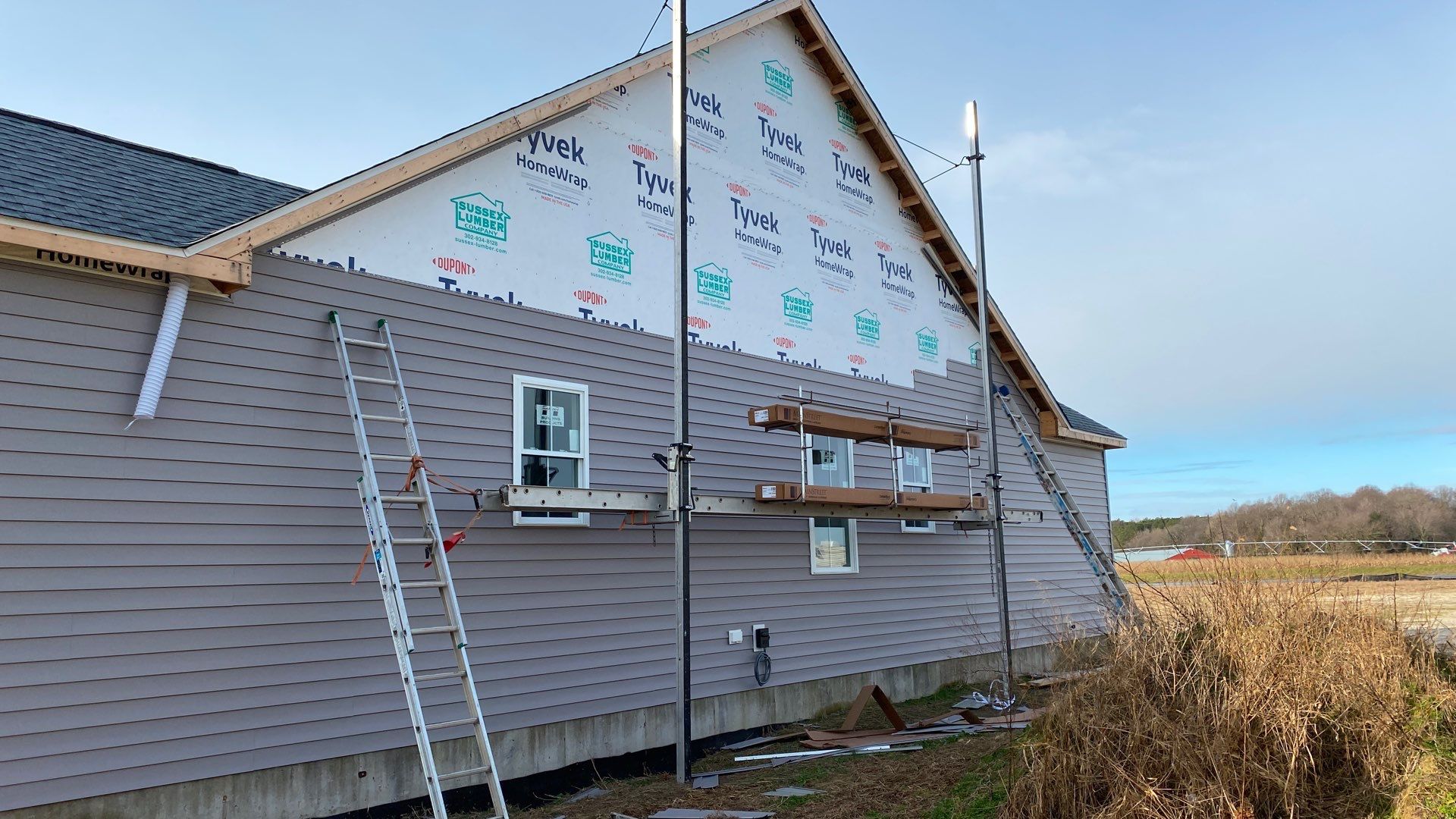
Insulated siding installation cost: Understanding the price of upgrading your home’s exterior is crucial. This involves more than just the materials; it’s about the labor, the complexity of your home’s structure, and the type of siding you choose. This guide helps you navigate these factors and make informed decisions.
From the initial assessment of your home’s needs to choosing the right contractor, the process can feel overwhelming. However, by breaking down the costs into manageable components—materials, labor, permits, and potential hidden expenses—you can gain a clearer picture of what to expect. This allows for better budgeting and a smoother renovation experience.
Factors Influencing Insulated Siding Installation Cost
Getting new insulated siding can significantly improve your home’s curb appeal and energy efficiency. However, the cost can vary widely. Understanding the factors that influence the price will help you budget effectively and make informed decisions. This section will break down the key elements that determine the final cost of your insulated siding installation.
Siding Material Costs
The type of siding you choose dramatically impacts the overall cost. Vinyl siding is generally the most affordable option, offering a balance of cost-effectiveness and durability. Fiber cement siding provides superior durability and fire resistance, but comes with a higher price tag. Metal siding, while exceptionally long-lasting and low-maintenance, is usually the most expensive choice. These differences reflect the material costs, manufacturing processes, and longevity of each option. For example, a vinyl siding project might cost significantly less per square foot than one using fiber cement or metal.
Labor Costs and Geographic Location
Labor costs are a substantial part of the total installation expense. These costs fluctuate based on geographic location. Areas with higher costs of living and a greater demand for skilled labor will naturally have higher installation fees. A project in a densely populated urban center will likely be more expensive than a similar project in a rural area due to higher labor rates and potentially increased travel time for contractors.
Installation Complexity
The complexity of the installation significantly influences the final cost. Removing existing siding adds time and labor, increasing the overall expense. Houses with intricate designs, multiple gables, or complex architectural features require more time and precision, thus resulting in higher labor charges. A simple, single-story home with a straightforward design will typically cost less to side than a multi-story home with dormers and other architectural details.
Siding Material | Average Cost per Square Foot | Factors Affecting Cost | Notes |
---|---|---|---|
Vinyl | $3-$8 | Material quality, labor costs, project complexity, regional variations | Wide range reflects diverse product quality and installation scenarios. |
Fiber Cement | $8-$15 | Material quality, labor costs (more specialized skills needed), project complexity, regional variations | More durable than vinyl, commands a higher price. |
Metal | $10-$20+ | Material quality (aluminum vs. steel), labor costs, project complexity, regional variations, specialized installation techniques | Longest lifespan, often requiring specialized installers. |
Breakdown of Installation Costs
Understanding the cost of insulated siding installation involves more than just the price of the materials. Several factors contribute to the overall expense, and a clear breakdown can help homeowners budget effectively and avoid unexpected surprises. This section details the typical costs associated with each stage of the process, potential hidden costs, and the cost differences between DIY and professional installation.
Material Costs
Material costs are a significant portion of the total project expense. These costs vary depending on the type of siding chosen (vinyl, fiber cement, etc.), its quality, and the quantity needed based on your home’s size and surface area. For example, vinyl siding is generally less expensive than fiber cement, but fiber cement offers superior durability and longevity. Additionally, the cost of insulation, flashing, and other necessary materials should be factored in. A rough estimate for materials might range from $3 to $15 per square foot, depending on the choices made.
Labor Costs
Labor costs are another substantial component. The hourly rate for professional installers varies geographically and based on experience and demand. The total labor cost depends on the complexity of the job, the size of the house, and the amount of prep work required (such as removing old siding). Expect to pay anywhere from $2 to $8 per square foot for labor, significantly impacting the overall budget.
Permitting Costs
Obtaining the necessary permits is a crucial step, though often overlooked. Permitting fees vary widely depending on local regulations and the scope of the project. These fees can range from a few hundred dollars to over a thousand, depending on location and project size. It’s important to check with your local building department early in the planning process to understand the specific requirements and associated costs.
Hidden Costs
Several hidden costs can significantly impact the final budget. These might include unexpected repairs needed during the removal of old siding (like rotted wood or damaged sheathing), disposal fees for old materials, unforeseen issues with the home’s structure, and potential changes to the original plan. Setting aside a contingency fund of 10-20% of the total estimated cost can help mitigate the financial impact of these unexpected expenses. For example, discovering extensive water damage behind the old siding could add thousands to the overall cost.
DIY vs. Professional Installation
While DIY installation might seem appealing to save on labor costs, it’s crucial to consider the potential downsides. Improper installation can lead to issues like leaks, energy inefficiency, and a less aesthetically pleasing result. Professional installers possess the expertise and experience to ensure a quality installation, minimizing the risk of these problems. While DIY might initially seem cheaper, the cost of potential mistakes could easily outweigh the savings. A typical scenario: a homeowner attempting DIY installation might save $5,000 in labor but incur $8,000 in repair costs due to improper installation leading to water damage.
Sample Budget for a Typical Home Siding Project
This is a sample budget and should be adjusted based on your specific home and chosen materials.
Item | Cost per Square Foot (Estimate) | Total Cost (1000 sq ft house example) |
---|---|---|
Materials (Siding, Insulation, Flashing) | $5 | $5,000 |
Labor | $4 | $4,000 |
Permits | $100 – $1000 | $500 (Average Estimate) |
Contingency (15%) | $1.35 | $1,350 |
Total Estimated Cost | $10,850 |
Siding Material Comparison and Cost Analysis
Choosing the right insulated siding material significantly impacts both the initial cost and the long-term expenses associated with your home’s exterior. Understanding the differences in lifespan, maintenance needs, and overall durability is crucial for making an informed decision. This comparison will help you weigh the pros and cons of popular siding options.
Insulated Siding Material Properties
The durability and longevity of insulated siding directly influence the overall installation cost. Materials with longer lifespans and lower maintenance needs often result in lower long-term costs, despite potentially higher upfront investment. Conversely, cheaper materials might require more frequent repairs and replacements, leading to higher overall expenses over time.
- Vinyl Siding: Vinyl siding is typically the most affordable upfront. It’s relatively easy to install and maintain, requiring only occasional cleaning. However, it’s susceptible to damage from impacts and extreme temperatures, potentially leading to shorter lifespan compared to other options (15-30 years). Its color can fade over time in intense sunlight. The lower initial cost is often offset by potential need for earlier replacement.
- Fiber Cement Siding: Fiber cement siding offers a superior balance of durability, longevity (50+ years), and aesthetic appeal. It’s more resistant to damage than vinyl and less prone to fading. While more expensive initially, its longer lifespan and lower maintenance requirements translate to lower long-term costs. Regular painting is required every 10-15 years to maintain its appearance and protection.
- Metal Siding: Metal siding, usually aluminum or steel, boasts exceptional durability and longevity (50+ years or more), surpassing both vinyl and fiber cement. It’s highly resistant to fire, insects, and extreme weather conditions. However, it’s generally the most expensive option upfront. Maintenance is minimal, primarily involving occasional cleaning and addressing any dents or scratches that may occur.
Cost and Longevity Relationship
The relationship between material durability and installation cost is generally inverse in the long term. While high-durability materials like metal siding have higher initial costs, their significantly longer lifespan and reduced maintenance needs often result in lower overall costs over the lifetime of the siding. Conversely, less durable materials like vinyl siding may initially save money, but the need for more frequent repairs and eventual replacement can quickly negate those initial savings. Consider a scenario where vinyl siding needs replacement every 20 years, while fiber cement lasts 50 years. The cumulative cost of multiple vinyl replacements might exceed the initial investment in fiber cement over the same period.
Finding and Hiring a Contractor
Choosing the right contractor is crucial for a successful insulated siding installation. A reputable contractor ensures quality workmanship, protects your investment, and minimizes potential headaches down the line. Taking the time to find the right fit will save you stress and money in the long run.
Finding a qualified contractor involves careful research and due diligence. This process should not be rushed, as the contractor you choose will significantly impact the final result and your overall satisfaction.
Contractor Selection Criteria
Selecting a contractor involves more than just comparing prices. Consider their experience, reputation, licensing, and insurance coverage. A thorough vetting process helps you make an informed decision.
Obtaining and Comparing Multiple Quotes
Getting at least three quotes from different contractors is essential for fair price comparison. Each quote should detail the scope of work, materials used, and payment schedule. Comparing quotes allows you to identify any discrepancies and negotiate favorable terms. For example, one contractor might offer a slightly higher price but include superior materials or a longer warranty.
Key Questions to Ask Potential Contractors
Before committing to a contractor, ask specific questions to assess their expertise and professionalism. These questions will help clarify their process and ensure alignment with your expectations. Examples include inquiring about their experience with similar projects, their approach to project management, and their warranty offerings. Asking about their preferred payment methods and schedule is also vital.
Verifying Contractor Licenses and Insurance
Verifying a contractor’s license and insurance is a critical step in protecting yourself from potential liabilities. Contact your state’s licensing board to confirm their credentials and ensure their license is current and valid. Request proof of liability and workers’ compensation insurance. This safeguards you from financial responsibility in case of accidents or damages during the installation process. For example, if a contractor’s worker is injured on your property, their insurance will cover medical expenses, preventing you from incurring unexpected costs.
Visual Representation of Installation Process
Insulated siding installation is a multi-step process requiring precision and attention to detail. Understanding these steps helps homeowners visualize the project and better communicate with contractors. This section provides a step-by-step guide, along with a method for calculating siding needs.
Siding Installation Steps
The installation process typically begins with preparation and ends with final touches. Each stage plays a crucial role in ensuring a long-lasting, aesthetically pleasing, and energy-efficient exterior.
- Preparation: This involves measuring the house’s exterior walls to determine the total square footage requiring siding. Existing siding removal (if necessary), cleaning the surface, and ensuring proper flashing and water management systems are in place are all crucial preparatory steps.
- Framing and Sheathing: If necessary, new framing may be installed to create a level surface for the siding. This step is particularly important when dealing with uneven walls or significant repairs. Proper sheathing ensures a solid foundation for the insulated siding.
- Insulation Installation: Insulation boards are attached directly to the sheathing. These boards provide thermal insulation, reducing energy costs and improving comfort. The type of insulation used will vary depending on climate and homeowner preference.
- Siding Installation: The insulated siding panels are installed over the insulation. This typically involves starting at a corner and working your way across the wall, ensuring proper overlapping and alignment of the panels. Special attention is paid to corners, windows, and doors.
- Trim and Finishing: Once the siding is in place, trim pieces are added to cover edges, corners, and around windows and doors, creating a neat and professional finish. Caulking is applied to seal any gaps, preventing water intrusion.
Calculating Total Square Footage
Accurately calculating the square footage is essential for ordering the correct amount of siding. This avoids unnecessary waste and ensures the project is completed efficiently.
To calculate the total square footage, measure the length and height of each wall section requiring siding. Multiply the length and height of each section, and then add the results together for all wall sections. Remember to account for doors and windows by subtracting their area from the total wall area. For example:
Total Square Footage = (Wall 1 Length x Wall 1 Height) + (Wall 2 Length x Wall 2 Height) + … – (Window Area) – (Door Area)
Visual Representation of the Process
Imagine the house as a three-dimensional model. First, you see the bare walls, possibly with old siding removed. Then, a layer of insulation boards is attached, creating a thermal barrier. Next, the insulated siding panels are meticulously placed, covering the insulation. Finally, trim pieces are added to create a clean, finished look. Each step builds upon the previous one, culminating in a fully insulated and aesthetically pleasing exterior. The process resembles building a layered cake, with each layer contributing to the final product’s strength, efficiency, and beauty. Key considerations include ensuring proper ventilation, water drainage, and alignment of panels for a seamless look.
Final Thoughts
Ultimately, the cost of insulated siding installation is a significant investment, but one that offers long-term benefits. By understanding the factors influencing the price and carefully planning your project, you can ensure a successful renovation that enhances your home’s curb appeal, energy efficiency, and overall value. Remember, a little research and planning go a long way in making this project a positive and rewarding experience.