Best Insulated Siding for Energy Savings
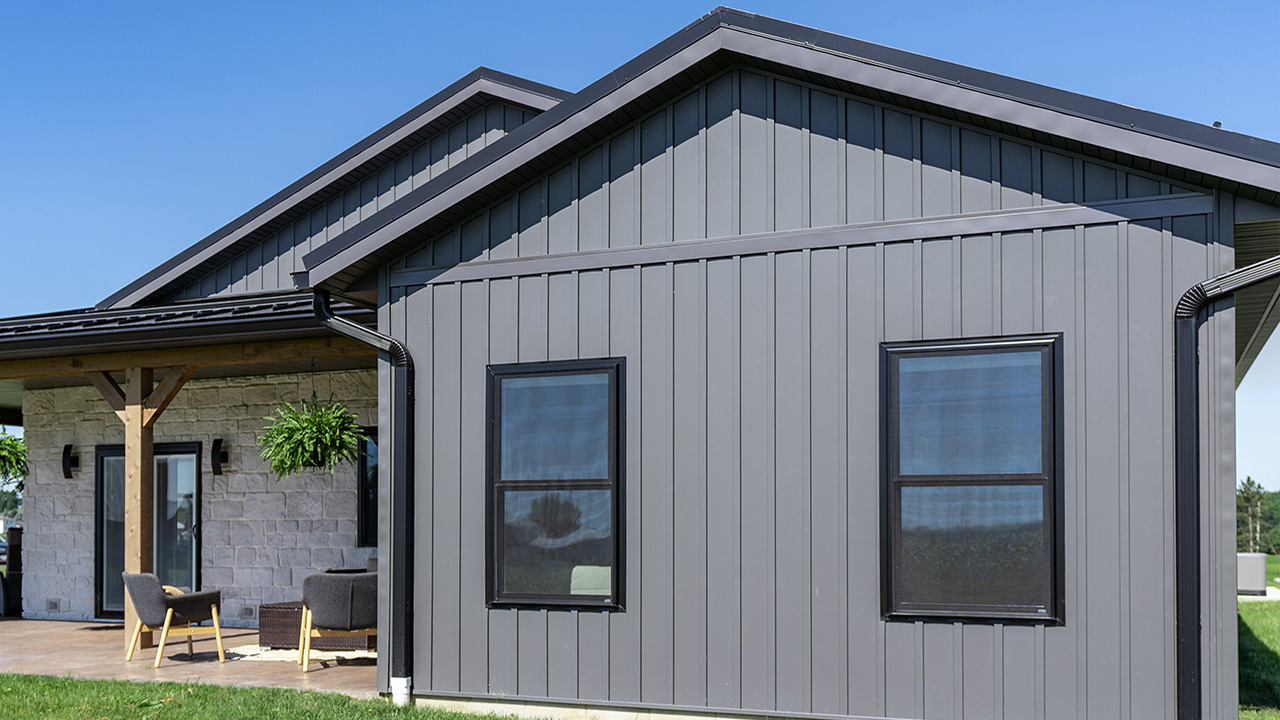
Best insulated siding for energy savings is more than just a pretty face; it’s a smart investment in your home’s comfort and your wallet. Choosing the right siding can significantly reduce energy bills, improve your home’s insulation, and even increase its resale value. This guide explores the various types of insulated siding, their performance, costs, and environmental impact, helping you make an informed decision for a warmer, more energy-efficient home.
We’ll delve into the specifics of different siding materials, from the R-value implications to installation considerations and long-term maintenance. Understanding these factors will empower you to select the best option for your climate, budget, and aesthetic preferences. We’ll also examine the environmental footprint of various siding choices, guiding you towards sustainable solutions that benefit both your home and the planet.
Types of Insulated Siding
Choosing the right insulated siding can significantly impact your home’s energy efficiency and curb appeal. Understanding the different types available is crucial for making an informed decision. This section details the various options, comparing their performance and maintenance needs.
Insulated Siding Materials
The market offers several types of insulated siding, each with unique properties. These differences affect both energy savings and long-term costs.
Siding Type | Material Composition | R-Value Range | Key Advantages |
---|---|---|---|
Foam-backed Vinyl Siding | Polyvinyl chloride (PVC) with a rigid foam insulation backing (typically polyurethane or polyisocyanurate). | R-2 to R-8 | Relatively inexpensive, low maintenance, wide variety of colors and styles, easy installation. |
Fiber Cement Siding with Foam Insulation | Cement, cellulose fibers, and sand, often with a foam insulation core or backing. | R-5 to R-10 (depending on thickness and foam type) | Durable, fire-resistant, low maintenance, can mimic the look of wood. |
Insulated Metal Siding | Steel or aluminum with a polyurethane or polyisocyanurate foam core. | R-8 to R-20 (depending on thickness and foam type) | Extremely durable, resistant to fire, insects, and rot, long lifespan. |
Polyurethane Siding | High-density polyurethane foam with a protective outer layer. | R-6 to R-8 | Excellent insulation properties, lightweight, easy to install. Often comes with factory-applied finishes. |
Thermal Performance Comparison
The R-value is a measure of a material’s resistance to heat flow. Higher R-values indicate better insulation. While foam-backed vinyl siding offers decent insulation, metal siding with a thick foam core generally provides the highest R-value, leading to superior energy savings. Fiber cement with foam insulation sits in the middle, offering a balance between insulation and durability. The actual R-value achieved will depend on the specific product and its installation. For example, a poorly installed high R-value siding system will perform worse than a well-installed lower R-value system.
Lifespan and Maintenance
The lifespan and maintenance requirements vary considerably among insulated siding types. Vinyl siding generally lasts 20-30 years with minimal maintenance, needing occasional cleaning. Fiber cement siding can last 50 years or more with proper care, requiring periodic painting or staining. Metal siding boasts an exceptionally long lifespan (50+ years) and is very low maintenance, mostly needing occasional cleaning. Polyurethane siding typically lasts 25-30 years and requires minimal upkeep, though occasional cleaning is advised. Regular inspection for any damage is recommended for all types to address issues promptly.
R-Value and Energy Efficiency
Understanding R-value is key to choosing the best insulated siding for your home. It’s a measure of how well a material resists the flow of heat, directly impacting your energy bills and home comfort. Higher R-values mean better insulation.
R-value’s impact on energy savings is significant because it determines how effectively your siding prevents heat from escaping in winter and entering in summer. This reduces the strain on your heating and cooling systems, leading to lower energy consumption and subsequently, lower utility bills. The higher the R-value of your siding, the less energy your home needs to maintain a comfortable temperature.
R-Value’s Contribution to Overall Home Energy Efficiency
The R-value of siding contributes to the overall thermal performance of your home’s exterior. While siding isn’t the only factor influencing energy efficiency (insulation in walls, windows, and roof also play crucial roles), it forms a significant part of the building envelope. A home with high R-value siding will experience less heat transfer through the walls, reducing the load on the HVAC system and minimizing energy waste. This translates to a smaller carbon footprint and increased comfort year-round.
R-Value, Climate Zone, and Energy Savings
The optimal R-value for your siding depends heavily on your climate zone. Homes in colder climates require higher R-values to effectively resist heat loss during winter. Conversely, homes in warmer climates may benefit from moderately high R-values to reduce heat gain during summer. For example, a home in Alaska would benefit significantly more from siding with a high R-value (e.g., R-15 or higher) compared to a home in Florida, where a lower R-value (e.g., R-7 or R-10) might suffice. Ignoring climate-specific R-value needs can lead to either energy waste or inadequate protection from the elements.
Impact of Varying R-Values on Energy Costs
The following table illustrates the potential impact of different R-values on annual energy costs for a typical 1500 sq ft home in various climate zones. These are estimates and actual savings will vary based on factors like home design, window efficiency, and heating/cooling system efficiency.
Climate Zone | R-Value of Siding | Estimated Annual Energy Cost Savings (USD) |
---|---|---|
Cold (e.g., Northern US) | R-7 | $100 – $200 |
Cold (e.g., Northern US) | R-15 | $300 – $600 |
Moderate (e.g., Midwestern US) | R-7 | $50 – $150 |
Moderate (e.g., Midwestern US) | R-11 | $150 – $300 |
Warm (e.g., Southern US) | R-7 | $25 – $75 |
Warm (e.g., Southern US) | R-10 | $75 – $150 |
Installation and Cost Considerations
Investing in insulated siding is a significant home improvement project, impacting both your home’s appearance and energy efficiency. Understanding the installation process and associated costs is crucial for making an informed decision. This section will guide you through the typical steps involved in installation and provide a cost comparison of different materials.
Insulated Siding Installation Process
Proper installation is key to maximizing the energy-saving benefits of insulated siding. A poorly installed system can lead to air leaks and reduced effectiveness. Following these steps ensures a professional and efficient installation.
- Preparation: This initial stage involves measuring the area to be sided, removing existing siding (if applicable), and preparing the underlying surface. This may include repairing damaged sheathing or addressing any moisture issues.
- Framing and Flashing: Installing proper flashing around windows, doors, and other openings is critical to prevent water penetration. This step helps create a weather-tight barrier.
- Siding Installation: Insulated siding panels are typically installed horizontally, starting at the bottom and working upwards. Each panel is carefully interlocked with the previous one to create a seamless and secure exterior.
- Trim and Finishing: Once the main siding is installed, trim pieces are added around windows, doors, and corners to create a finished look. This step adds to the overall aesthetic appeal of the project.
- Inspection and Cleanup: A final inspection ensures all panels are properly installed and sealed. Any necessary repairs are made, and the work area is thoroughly cleaned.
Cost Comparison of Insulated Siding Materials
The cost of insulated siding varies significantly depending on the material chosen. Fiber cement and vinyl are common choices, each with its own price point and advantages. Engineered wood siding offers another option, but often at a higher cost. Labor costs also play a significant role in the overall project expense. For example, a complex installation with many corners and angles will generally be more expensive than a simple, flat-sided installation.
Potential Hidden Costs
While the upfront costs of materials and labor are significant, several hidden costs can unexpectedly increase the overall project expense.
- Permitting Fees: Building permits are often required for exterior home renovations, adding to the overall project cost. The cost varies by location and the scope of the project.
- Unexpected Repairs: During the removal of existing siding, underlying problems like rotted wood or water damage may be discovered, requiring additional repairs and increasing expenses.
- Waste Removal: Disposal of old siding and other construction debris can add unexpected costs, especially if special handling is required for hazardous materials.
- Material Adjustments: Slight variations in wall dimensions or unforeseen issues may require additional materials, pushing the total cost higher.
Insulated Siding Cost Comparison
Siding Type | Material Cost (per sq ft) | Labor Cost (per sq ft) | Total Cost (per sq ft) |
---|---|---|---|
Vinyl | $3 – $8 | $3 – $6 | $6 – $14 |
Fiber Cement | $8 – $15 | $4 – $8 | $12 – $23 |
Engineered Wood | $12 – $25 | $5 – $10 | $17 – $35 |
Environmental Impact and Sustainability
Choosing insulated siding involves more than just energy efficiency; it’s also about considering the environmental footprint of the product throughout its lifecycle. From manufacturing to disposal, the materials used significantly impact our planet. Understanding this impact helps make informed, sustainable choices.
The environmental impact of insulated siding hinges on the materials used in its construction. Different materials have varying degrees of impact on resource depletion, air and water pollution, and greenhouse gas emissions. Factors such as energy consumption during manufacturing, transportation distances, and end-of-life disposal methods all contribute to the overall environmental scorecard.
Embodied Carbon Footprint of Insulated Siding
The embodied carbon footprint represents the total greenhouse gas emissions associated with a product’s entire lifecycle, from raw material extraction to manufacturing, transportation, installation, and finally, disposal. For insulated siding, this footprint varies considerably depending on the primary material. For example, fiber cement siding generally has a lower embodied carbon footprint than vinyl siding due to the use of more sustainable raw materials and manufacturing processes. However, the specific footprint is also influenced by the manufacturing process and the distance the product travels from factory to installation site. A study by the University of California, Berkeley, for instance, compared the embodied carbon of various building materials, highlighting the significant differences between materials like wood and concrete. These findings can be extrapolated to understand the relative impact of different insulated siding options.
Sustainable Sourcing and Manufacturing Practices
Several manufacturers are actively pursuing sustainable practices in the production of insulated siding. These practices include using recycled materials in the manufacturing process, sourcing timber from responsibly managed forests (certified by organizations like the Forest Stewardship Council), and implementing energy-efficient manufacturing processes to reduce greenhouse gas emissions. Some manufacturers also focus on minimizing water usage and waste generation during production. For instance, a company might use recycled plastic in the production of vinyl siding, thereby reducing reliance on virgin materials. Another might invest in renewable energy sources to power their factories, reducing their carbon footprint. The use of locally sourced materials can also contribute to sustainability by minimizing transportation distances and associated emissions.
Disposal and Recycling of Insulated Siding
The end-of-life management of insulated siding also significantly impacts the environment. The disposal of some materials, such as vinyl siding, can contribute to landfill waste. However, some manufacturers offer recycling programs for their products, and some types of siding, like fiber cement, are more easily recycled than others. It’s crucial to research the disposal options and recycling programs available for the specific type of insulated siding being considered. Proper disposal and recycling practices are vital in minimizing the environmental impact of insulated siding at the end of its useful life. For example, some communities offer curbside pickup for specific types of building materials, while others may have dedicated recycling centers for construction debris.
Insulated Siding and Home Aesthetics
Choosing insulated siding isn’t just about energy efficiency; it’s a significant aesthetic decision that impacts your home’s curb appeal and overall value. The right siding can dramatically enhance your home’s appearance, transforming it from ordinary to extraordinary. The material you select, along with its color and texture, plays a crucial role in achieving the desired look.
Insulated siding offers a wide array of options to complement various architectural styles and personal preferences. Different materials offer unique visual characteristics, influencing the overall feel and style of your home. Consider the existing architectural features, landscaping, and neighborhood context when making your selection.
Siding Material Appearance
The visual impact of insulated siding varies greatly depending on the material. Fiber cement, for instance, offers a clean, crisp look that can be painted in a wide range of colors, mimicking the appearance of wood or stucco. Vinyl siding, while more affordable, provides a smoother, more uniform appearance, often available in a variety of colors and textures to simulate wood grain or other patterns. Engineered wood siding offers a natural wood aesthetic without the high maintenance. Metal siding, particularly aluminum or steel, provides a modern, sleek appearance often favored in contemporary designs.
Color, Texture, and Style Options
The color, texture, and style of your insulated siding are key elements in shaping your home’s aesthetic. Careful consideration of these factors can significantly enhance your home’s curb appeal.
- Classic Styles: Think of traditional clapboard siding, often seen in white or muted earth tones. This style evokes a sense of timeless elegance and blends well with traditional architectural styles. The texture is typically smooth with subtle vertical lines, offering a clean and understated look.
- Modern Styles: Modern designs often feature large, horizontal panels in sleek colors like charcoal gray, deep blues, or even bold reds. The textures might be smoother, almost seamless, or feature subtle metallic accents for a contemporary feel.
- Rustic Styles: Rustic styles utilize textures that mimic natural materials like wood or stone. Colors tend to be warm and earthy, such as browns, greens, and creams. The siding might have a rougher texture to enhance the rustic appearance, often incorporating variations in color and shading.
- Contemporary Styles: Contemporary homes might feature smooth, brightly colored siding with clean lines. Colors can range from vibrant jewel tones to muted pastels, reflecting the home’s modern and minimalist design.
Siding Selection for Architectural Styles
Selecting insulated siding that complements your home’s architectural style is crucial for maintaining its aesthetic integrity.
A Victorian home, with its intricate details and ornate features, might be best complemented by fiber cement siding painted in a deep, rich color to highlight its architectural details. A ranch-style home, characterized by its low-pitched roof and horizontal lines, would benefit from horizontal siding in a muted earth tone. A contemporary home with its clean lines and minimalist design might pair well with smooth, large-panel siding in a bold, modern color. A craftsman-style home, known for its natural materials and handcrafted details, could benefit from engineered wood siding in a natural wood finish.
Case Studies
Real-world examples demonstrate the tangible benefits of insulated siding. These case studies highlight the significant energy savings and increased homeowner satisfaction achieved through the installation of various insulated siding options. The data presented showcases the potential for substantial return on investment and improved comfort.
Case Study 1: The Miller Family Home
The Miller family, residing in a suburban area of Minneapolis, Minnesota, experienced harsh winters with significant temperature fluctuations. Their older home, originally clad in outdated wood siding, suffered from significant heat loss. After installing vinyl insulated siding with an R-value of 4, their annual heating costs decreased by approximately 30%. The Millers reported a noticeably warmer and more comfortable home, significantly reducing their reliance on supplemental heating sources. The improved energy efficiency also contributed to a more stable indoor temperature, enhancing their overall quality of life.
Case Study 2: The Rodriguez Residence
Located in Phoenix, Arizona, the Rodriguez family’s home faced the challenge of intense summer heat. Their previous stucco siding offered minimal insulation, resulting in high cooling costs. They opted for fiber cement insulated siding with an R-value of 6. This upgrade led to a remarkable 25% reduction in their annual cooling expenses. The cooler indoor temperatures improved the comfort of the home, especially during the peak summer months. The homeowners also noted a reduction in fading and damage to their interior furnishings due to the improved temperature regulation.
Case Study 3: The Chen Family Home
The Chen family, living in a coastal area of Charleston, South Carolina, sought to improve the energy efficiency of their home while enhancing its aesthetic appeal. They chose insulated engineered wood siding with an R-value of 5. This choice not only provided excellent insulation, reducing their energy bills by approximately 18%, but also offered a durable and visually appealing exterior. The Chen family reported significant satisfaction with both the energy savings and the enhanced curb appeal of their home, showcasing the multifaceted benefits of insulated siding.
Conclusion
Ultimately, selecting the best insulated siding involves balancing energy efficiency, cost, aesthetics, and environmental considerations. By carefully weighing the pros and cons of different materials and understanding your individual needs, you can make a choice that enhances your home’s value, comfort, and sustainability. Investing in energy-efficient siding is an investment in a brighter, more comfortable, and more environmentally responsible future for your home and family.