Insulated Siding Cost Per Square Foot
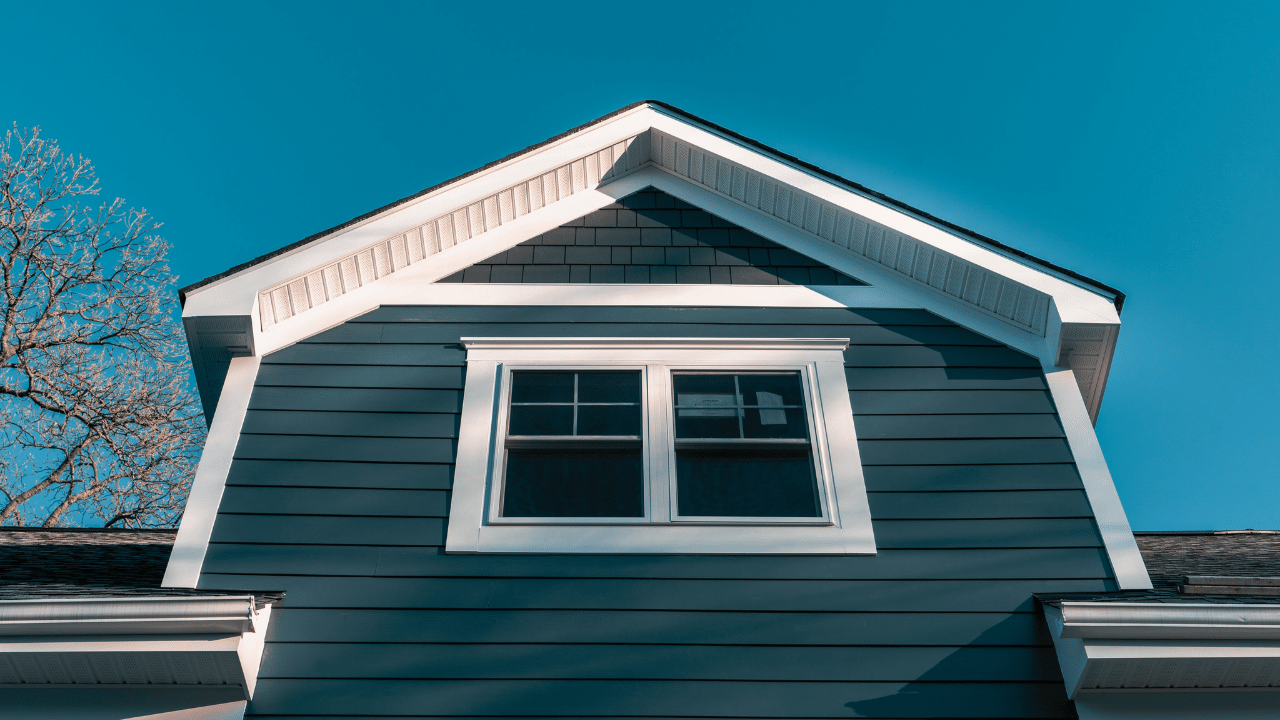
Insulated siding cost per square foot varies greatly depending on the material chosen, your location, and the complexity of your project. Understanding these factors is key to budgeting effectively for a home improvement that offers both aesthetic appeal and significant long-term energy savings. This guide will explore the different costs associated with insulated siding, helping you make informed decisions for your home.
We’ll delve into the specifics of various materials like vinyl, fiber cement, and metal, examining their price ranges and comparing their cost-effectiveness. We’ll also cover crucial installation costs, including labor, permits, and potential unexpected expenses. Finally, we’ll highlight the substantial energy savings you can expect, illustrating how insulated siding can provide a significant return on investment over time.
Average Costs
Insulated siding offers a significant boost to your home’s energy efficiency and curb appeal. However, the cost can vary considerably depending on several factors. Understanding these variations is key to making an informed decision. This section will explore the average costs associated with different types of insulated siding.
The price you pay for insulated siding is influenced by a number of interconnected elements. Material choice plays a crucial role, with vinyl generally being the most affordable and fiber cement or metal options commanding higher prices. Your geographic location also impacts the overall cost, as labor rates and material availability fluctuate regionally. Finally, the thickness of the siding material itself directly affects the price; thicker materials typically cost more but provide superior insulation.
Insulated Siding Cost Breakdown by Material
The following table provides a general range of costs per square foot for different insulated siding materials. Remember that these are estimates, and actual costs can vary significantly based on the factors discussed above. Always obtain multiple quotes from reputable contractors in your area.
Material | Low Cost ($/sq ft) | Average Cost ($/sq ft) | High Cost ($/sq ft) |
---|---|---|---|
Vinyl | 3 | 5 | 8 |
Fiber Cement | 7 | 12 | 18 |
Metal | 8 | 15 | 25 |
Factors Influencing Cost Variations
Several factors contribute to the wide range in insulated siding costs. Understanding these helps in budgeting accurately and avoiding surprises during the project.
Geographic Location: Labor costs, material transportation, and local market demand all influence pricing. For example, siding installation in a densely populated urban area might be more expensive due to higher labor rates compared to a rural area. Similarly, areas prone to extreme weather conditions may require more robust materials, adding to the cost.
Labor Rates: The cost of labor can vary significantly depending on the contractor’s experience, location, and demand. Experienced installers typically charge more but may offer higher quality workmanship and faster project completion. It is important to compare quotes from several contractors to find a balance between price and quality.
Impact of Material Thickness on Cost
The thickness of the siding material directly correlates with its cost and insulation value. Thicker materials generally offer better insulation, leading to lower energy bills in the long run. However, this improved performance comes at a higher upfront cost. For example, a thicker fiber cement board will provide superior insulation and durability compared to a thinner one, but this translates to a higher price per square foot.
Consider the long-term savings from improved energy efficiency when comparing costs. While a thicker, more expensive material might have a higher initial investment, the reduced energy bills over the siding’s lifespan could offset the extra cost. This is a crucial factor to consider when weighing the cost versus the benefits of different material thicknesses.
Material-Specific Costs
Choosing the right insulated siding depends heavily on your budget and desired aesthetic. Different materials offer varying levels of cost-effectiveness, longevity, and maintenance requirements. Understanding the price per square foot for each option, including installation, is crucial for informed decision-making.
Vinyl Insulated Siding Costs
Vinyl insulated siding offers a balance of affordability and decent insulation properties. The cost per square foot, including professional installation, typically ranges from $8 to $15. This variation stems from factors such as siding thickness, style, and the installer’s labor rates. Higher-end vinyl siding with thicker panels and more intricate designs naturally commands a higher price. Remember that this cost is just an estimate, and you should always obtain multiple quotes from reputable contractors in your area for a precise project cost.
Vinyl Siding Cost Comparison
The following table compares the cost per square foot of different grades and brands of vinyl insulated siding, including professional installation. These are average figures and can fluctuate based on regional differences and specific product features.
Brand/Grade | Cost per Square Foot (Installation Included) | Thickness (Inches) | Features |
---|---|---|---|
Economy Vinyl | $8 – $10 | 0.04 – 0.05 | Basic designs, limited color options |
Mid-Range Vinyl | $10 – $13 | 0.05 – 0.06 | More color and style choices, improved durability |
Premium Vinyl | $13 – $15 | 0.06 – 0.08 | Enhanced durability, wider range of styles and colors, potential for added features like impact resistance |
Fiber Cement Insulated Siding Costs
Fiber cement insulated siding offers superior durability and fire resistance compared to vinyl. However, it comes with a significantly higher price tag. The cost per square foot, including installation, generally ranges from $15 to $30, or even more for premium brands and intricate designs. The variation depends on the siding profile, thickness, and the complexity of the installation.
For example, a simple lap siding profile might fall at the lower end of this range, while more complex styles like shake or shingle profiles will be more expensive. A homeowner might choose a simple lap profile for a more budget-friendly approach, while a homeowner looking for a more upscale look might choose a more detailed shingle profile, accepting the higher price.
Metal Insulated Siding Cost-Effectiveness
Metal insulated siding, typically made of aluminum or steel, presents a unique proposition. While its initial cost per square foot (including installation) is often comparable to or slightly higher than fiber cement, ranging from $18 to $35, its exceptional longevity and minimal maintenance needs contribute to long-term cost-effectiveness. The extended lifespan and reduced maintenance costs often outweigh the higher upfront investment over the life of the siding. For example, a homeowner might spend more initially on metal siding, but avoid the need for costly repairs or replacements that could be necessary with vinyl or fiber cement siding over several decades.
Installation Costs
Insulated siding installation costs are a significant factor in your overall project budget. Understanding these costs, which vary widely based on location, project size, and installer expertise, is crucial for accurate planning. This section breaks down the components of installation costs and provides a guide to the process itself.
Installation costs typically represent a substantial portion of the total project expense, often exceeding the cost of the materials themselves. Factors such as the complexity of the project, the size of the house, and the installer’s experience all play a significant role in determining the final price. Regional differences in labor rates also contribute to the variability in costs.
Hourly and Daily Rates for Siding Installers
Hourly or daily rates for siding installers vary considerably depending on geographic location and the installer’s experience and reputation. In some areas with a high cost of living, like major cities on the US coasts, experienced installers might charge $50-$80 per hour or $400-$600 per day. In less populated areas of the Midwest or South, rates might range from $30-$50 per hour or $250-$400 per day. These are estimates and should be verified with local contractors for accurate pricing.
Breakdown of Installation Costs
The total installation cost comprises several key elements. A detailed breakdown will help you understand where your money is going. It’s essential to obtain itemized quotes from multiple installers to compare and choose the best value.
- Labor Costs: This is the largest portion of the installation cost, encompassing the time and expertise of the installation crew. The complexity of your house’s design and the amount of prep work needed will affect labor costs.
- Material Costs: This includes the cost of the insulated siding panels, fasteners, flashing, and any additional trim or accessories needed. Material costs are usually separately itemized in a quote.
- Permitting Fees: Building permits are usually required for exterior renovations. The cost varies widely based on local regulations and the project’s scope. These costs should be included in the total project estimate.
- Waste Removal: Disposal of old siding and construction debris is an additional cost that should be factored in. Some installers include this in their quote, while others charge separately.
- Contingency: It’s wise to include a contingency of 10-15% of the total estimated cost to account for unforeseen expenses or delays.
Step-by-Step Installation Guide
The installation process for insulated siding is a multi-step procedure requiring skill and precision. The following steps provide a general overview; always refer to the manufacturer’s instructions for your specific siding product.
- Preparation: This stage involves removing the old siding, repairing any underlying damage to the sheathing, and ensuring the surface is clean and level. Image description: A house with the old siding partially removed, revealing the underlying wood sheathing. Workers are using tools to carefully remove the old materials, ensuring they don’t damage the house’s structure.
- Framing and Flashing: Install any necessary flashing around windows and doors to prevent water penetration. Straight, sturdy framing is essential for a professional-looking finish. Image description: Close-up of a window frame with flashing properly installed to protect against water damage. The flashing is neatly sealed around the frame, preventing gaps.
- Siding Installation: Start at the bottom of the wall and work your way up, overlapping each panel according to the manufacturer’s instructions. Use appropriate fasteners to secure the panels firmly. Image description: A worker installing an insulated siding panel, using a level to ensure it is straight and properly aligned. The panel is being secured with specialized fasteners.
- Trim and Finishing: Install trim around windows, doors, and corners to complete the installation. Ensure all seams and joints are properly sealed to prevent water leakage. Image description: The completed siding installation, showing neatly installed trim around windows and doors. The siding is uniformly aligned, and the overall appearance is clean and professional.
Additional Factors Affecting Cost
Insulated siding costs aren’t just about square footage; several other factors significantly influence the final price. Understanding these variables helps homeowners budget accurately and avoid unexpected expenses. This section explores some key elements that impact the overall cost of your insulated siding project.
Home Size and Complexity Influence on Cost
The size of your home directly correlates with the amount of siding needed, thus impacting the overall cost. Larger homes naturally require more materials and labor, leading to higher expenses. Beyond sheer size, the complexity of your home’s architecture plays a crucial role. Homes with numerous angles, dormers, or intricate designs require more meticulous cutting and fitting of the siding, increasing both material and labor costs. For example, a simple ranch-style home will likely cost less than a Victorian-style home with its many gables and decorative features. The additional time and precision needed for complex designs translate into a higher final bill.
Existing Siding Removal Costs
Removing existing siding before installing new insulated siding adds a considerable expense to the project. This process involves labor costs for careful removal to avoid damage to underlying walls and proper disposal of the old siding. The cost varies depending on the type of existing siding (e.g., vinyl, wood, brick) and its condition. Removing aged or damaged siding can be more time-consuming and potentially more expensive due to the increased risk of unforeseen complications. For instance, removing asbestos-containing siding necessitates specialized handling and disposal procedures, significantly increasing the cost.
Specialized Features and Associated Costs
Specialized features like trim, corners, and flashing add to the overall cost of insulated siding installation. These elements are essential for a professional-looking and weather-tight finish. Trim pieces, such as window and door casings, require precise measurements and installation, increasing labor costs. Corners require specially designed siding pieces for a clean and seamless appearance. Flashing, crucial for preventing water damage around windows and other openings, also adds to the material and installation expenses. The more elaborate the trim work and the more complex the home’s design, the higher the cost of these specialized components.
Repair and Unexpected Issue Costs
Unforeseen repairs or issues during installation can unexpectedly inflate the project’s cost. These might include discovering rotted wood under the existing siding, requiring extensive repairs before new siding can be installed. Other unexpected issues could involve problems with the existing wall structure, needing additional work to ensure a secure and stable base for the new siding. These unforeseen expenses highlight the importance of thorough inspections before starting the project and selecting a reputable contractor who can accurately assess potential problems and provide transparent cost estimates. For example, discovering termite damage necessitates specialized treatment before siding installation can proceed, adding significant cost and time delays.
Long-Term Cost Savings
Investing in insulated siding offers significant long-term cost savings, primarily through reduced energy bills. The superior insulation properties of these materials help maintain a consistent indoor temperature, minimizing the workload on your heating and cooling systems. This translates to lower energy consumption and, consequently, a smaller monthly energy bill. Over the lifespan of the siding, these savings can substantially offset the initial investment cost.
The energy savings generated by insulated siding can be substantial, leading to a positive return on investment over time. For example, a homeowner in a climate with extreme temperature fluctuations might see a reduction in heating costs by 20-30% annually. This reduction could easily amount to several hundred dollars per year, depending on the size of the home and the energy efficiency of the existing heating system. Imagine a family saving $500 annually – that’s $5000 over a decade, a significant portion of the initial siding investment.
Energy Bill Reduction Over Time
The following table illustrates the potential reduction in energy bills over a 15-year period for a typical home, comparing insulated siding to traditional vinyl siding. These figures are estimates and will vary depending on factors such as climate, home size, and energy usage habits.
Year | Annual Energy Cost (Traditional Siding) | Annual Energy Cost (Insulated Siding) | Annual Savings |
---|---|---|---|
1 | $1800 | $1440 | $360 |
5 | $1800 | $1440 | $360 |
10 | $1800 | $1440 | $360 |
15 | $1800 | $1440 | $360 |
Lifespan and Maintenance of Insulated Siding Materials
Different insulated siding materials have varying lifespans and maintenance requirements. Understanding these differences is crucial for making an informed decision. Proper maintenance extends the lifespan and maintains the energy efficiency of any siding.
For example, fiber cement insulated siding generally boasts a lifespan of 50 years or more with minimal maintenance, needing only occasional cleaning. Vinyl insulated siding typically lasts 20-30 years and requires periodic cleaning to maintain its appearance. While requiring less initial investment, vinyl may need replacing sooner, negating some of the initial cost savings over the long term. Metal insulated siding offers a very long lifespan (50+ years) with low maintenance needs, similar to fiber cement, but comes with a higher initial cost. Regular inspection and cleaning for all types of insulated siding are vital for preserving their energy-saving properties and extending their lifespan.
Closure
Ultimately, the cost of insulated siding per square foot is a multifaceted investment. While the initial expense may seem significant, the long-term energy savings and increased home value often outweigh the upfront costs. By carefully considering the factors discussed—material type, installation costs, and long-term benefits—you can make an informed decision that best suits your budget and enhances your home’s comfort and value for years to come. Remember to always get multiple quotes from reputable contractors to ensure you’re getting the best possible price.