Insulated Siding Repair Tips: A Homeowners Guide
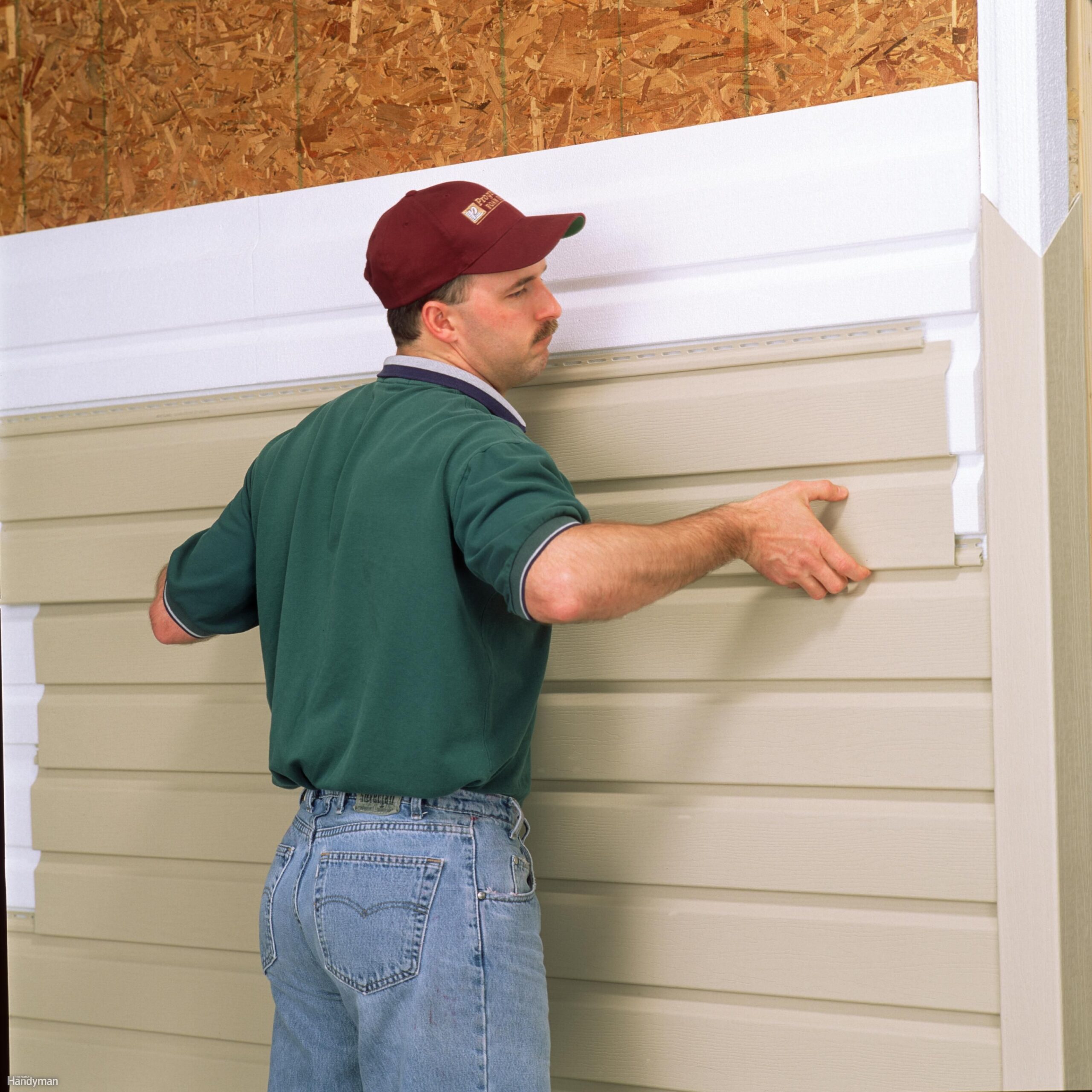
Insulated siding repair tips can save you money and keep your home looking its best. Understanding how to identify and fix damage, from small cracks to major panel replacements, is crucial for maintaining your home’s curb appeal and protecting it from the elements. This guide will walk you through the process, offering practical advice and solutions for common problems, empowering you to tackle repairs with confidence.
We’ll cover everything from assessing the damage and choosing the right repair materials to preventing future problems and dealing with more serious issues like water damage. Whether you’re a seasoned DIYer or a complete beginner, this comprehensive guide will provide you with the knowledge and steps needed to successfully repair your insulated siding.
Identifying Damage to Insulated Siding
Insulated siding, while durable, is susceptible to various types of damage over time. Regular inspection is key to preventing minor issues from escalating into costly repairs. Understanding the common types of damage and how to assess their severity is crucial for effective maintenance.
Common types of damage include cracks, gaps, dents, water damage (leading to rot or mold), and discoloration. These issues can stem from several sources, including impact from debris, severe weather, improper installation, or simply age and wear. Careful inspection will help pinpoint the problem areas and their underlying causes.
Inspecting Insulated Siding for Damage
A thorough inspection involves a visual examination of the entire siding surface. Begin by checking for any visible cracks or gaps between the panels. Look closely for any signs of water damage, such as discoloration, swelling, or soft spots. Pay close attention to areas prone to water accumulation, like corners, seams, and around windows and doors. Use a flashlight to inspect hard-to-see areas, and carefully examine the caulking around any penetrations in the siding. Note the location and extent of any damage observed.
Assessing the Severity of Damage
The severity of damage is determined by the size and extent of the problem. Small cracks or minor dents may only require minor repairs, while significant damage, such as large cracks, extensive water damage, or missing sections, may necessitate replacing entire panels. If water damage is suspected, gently probe the affected area to check for softness or sponginess, indicating potential rot. Document your findings, including photographs, to help with planning repairs.
Identifying the Underlying Cause of Damage
Once the damage is assessed, determining the underlying cause is essential for preventing future problems. For example, cracks might indicate impact damage from hail or tree branches, while gaps could point to improper installation or movement of the underlying structure. Water damage frequently indicates a problem with flashing, caulking, or drainage. By identifying the root cause, you can take appropriate steps to address the issue and prevent recurrence. For instance, loose or improperly installed flashing around windows could allow water penetration, leading to rot behind the siding. Identifying and correcting this flashing issue is crucial to prevent further damage. Similarly, gaps between panels might indicate that the siding wasn’t properly fastened during installation, necessitating re-fastening or replacement.
Repairing Minor Damage to Insulated Siding
Minor damage to your insulated siding, such as small cracks or holes, is often easily repairable with the right approach. Addressing these issues promptly prevents further damage and maintains your home’s curb appeal. This section will guide you through the process of repairing these imperfections, ensuring a lasting and seamless fix.
Careful preparation is key to a successful repair. Cleaning the damaged area removes dirt, debris, and any loose material, creating a clean surface for better adhesion of the patching compound. This ensures a strong and lasting repair that won’t easily crack or peel. Using a stiff brush, gently scrub the area to remove loose particles. Then, use a clean cloth dampened with water to wipe away any remaining residue. Allow the area to dry completely before applying any repair material.
Applying Caulk or Patching Compound
Applying caulk or patching compound requires a steady hand and the right technique. Begin by applying a small amount of the chosen material to the damaged area, using a caulking gun for caulk or a putty knife for patching compounds. Work the material into the crack or hole, ensuring complete filling. Use a smoothing tool, such as a wet finger or a putty knife, to create a smooth, even surface. Avoid applying too much pressure, which could force the material out of the crack and create an uneven finish. Let the material dry completely according to the manufacturer’s instructions before painting, if necessary.
Suitable Repair Materials
Several materials effectively patch insulated siding. Caulk, available in various colors, provides a flexible solution for smaller cracks. Acrylic latex caulk is a popular choice due to its durability and ease of application. For larger holes or more significant damage, patching compounds offer a more substantial repair. These compounds are often available in matching colors to blend seamlessly with your siding. When choosing, consider the color of your siding and opt for a material with similar properties in terms of flexibility and durability to ensure a long-lasting, unnoticeable repair. For instance, if your siding is a light gray, selecting a light gray patching compound would provide the most seamless repair. Always check the manufacturer’s instructions for specific application details and drying times.
Replacing Damaged Insulated Siding Panels
Replacing a damaged insulated siding panel might seem daunting, but with the right tools and a methodical approach, it’s a manageable DIY project. This process involves carefully removing the old panel, measuring for a replacement, and securely installing the new one, ensuring a seamless and weatherproof finish.
Tools and Materials Required
Gathering the necessary tools and materials beforehand streamlines the replacement process and prevents interruptions. Having everything readily available ensures a smoother and more efficient repair.
- Measuring tape
- Utility knife or siding cutter
- Pry bar or flathead screwdriver
- Hammer
- Caulk gun
- Replacement insulated siding panel
- Appropriate fasteners (nails, screws, or clips, depending on the siding type)
- Safety glasses
- Work gloves
- Caulk (exterior-grade, paintable)
Removing the Damaged Panel
Careful removal of the damaged panel minimizes the risk of further damage to surrounding siding and underlying structure. This step requires patience and attention to detail to avoid unnecessary complications.
- Carefully pry away the damaged panel from the surrounding panels, starting at one corner. Use a pry bar or flathead screwdriver to gently lift the panel without causing damage to the adjacent sections.
- Once you’ve loosened one edge, work your way along the panel, carefully removing fasteners as you go. Be cautious not to damage the adjacent panels or underlying structure.
- Once the panel is completely loose, remove it carefully. Inspect the area behind the panel for any underlying damage that needs repair before installing the new panel.
Measuring and Cutting the Replacement Panel
Accurate measurements are crucial for a perfect fit and a professional-looking repair. Improper measurements can lead to gaps, which compromise the weatherproofing and aesthetics of the siding.
- Carefully measure the width and height of the opening where the damaged panel was located. Note: It’s crucial to measure multiple times to ensure accuracy.
- Transfer these measurements to the replacement panel. Use a pencil to mark the cutting lines clearly.
- Use a utility knife or siding cutter to carefully cut the replacement panel to the measured dimensions. A straight edge and a sharp blade are essential for clean cuts.
- Double-check the dimensions of the cut panel against the opening before installation to ensure a precise fit.
Installing the Replacement Panel
The installation of the new panel is the final step, requiring attention to detail and secure fastening to ensure long-lasting performance and weather resistance. Proper installation is critical for maintaining the integrity of the siding system.
- Carefully align the new panel with the surrounding panels. Ensure it is properly positioned before fastening.
- Secure the panel using the appropriate fasteners (nails, screws, or clips) following the manufacturer’s instructions. Even spacing is essential for a neat and secure fit.
- Apply a bead of exterior-grade caulk along the edges of the new panel where it meets the adjacent panels to seal any gaps and prevent water infiltration.
Fastening Methods Comparison
Method | Advantages | Disadvantages | Tools Required |
---|---|---|---|
Nails | Cost-effective, readily available. | Can be prone to loosening over time, requires precise placement. | Hammer, nail set |
Screws | Stronger hold, easier to remove and replace if needed. | More expensive than nails, requires a screwdriver. | Screwdriver, possibly drill |
Clips | Concealed fastening, clean aesthetic appearance. | Can be more expensive, requires specific clips for the siding type. | Hammer or pliers (depending on clip type) |
Adhesive | Strong bond, suitable for smaller panels or repairs. | Requires precise application, less forgiving of errors. | Caulk gun, possibly scraper for excess adhesive. |
Preventing Future Insulated Siding Damage
Protecting your investment in insulated siding involves more than just repairing damage; it requires proactive maintenance to ensure its longevity and beauty. Regular care will not only prevent costly repairs but also maintain your home’s curb appeal for years to come. A little preventative care goes a long way in preserving the integrity of your siding.
Regular cleaning and inspection are fundamental to preventing significant damage to your insulated siding. Dirt, debris, and mold can accumulate over time, compromising the siding’s protective layers and potentially leading to warping, cracking, or discoloration. Annual inspections, ideally in spring and fall, allow you to identify and address minor issues before they escalate into major problems. A thorough cleaning removes these contaminants, restoring the siding’s appearance and protecting it from further deterioration.
Cleaning Insulated Siding
Choosing the right cleaning method depends heavily on your siding’s material. Using abrasive cleaners or inappropriate techniques can damage the siding’s surface, negating the benefits of your efforts. For vinyl siding, a gentle solution of mild dish soap and water, applied with a soft-bristled brush, is usually sufficient. Rinse thoroughly with a garden hose to remove all soap residue. For fiber cement siding, a pressure washer can be effective, but use a low-pressure setting to avoid damaging the surface. Always test any cleaning solution on a small, inconspicuous area first to ensure it doesn’t cause discoloration or damage. Never use harsh chemicals, bleach, or abrasive scrub brushes, as these can scratch or dull the finish. For aluminum siding, a similar approach to vinyl is recommended: mild soap and water, followed by thorough rinsing.
Protecting Insulated Siding from Weather
Extreme weather conditions pose significant threats to insulated siding. Intense sunlight can cause fading and warping, while heavy rain and snow can lead to water damage. Regularly inspect for any signs of loose or damaged panels, particularly after severe weather events. Consider installing gutters and downspouts to divert water away from the foundation and siding. Trimming overhanging trees and shrubs will help prevent moisture buildup and reduce the risk of branches impacting the siding. In areas prone to heavy snowfall, ensure proper drainage to prevent water accumulation behind the siding. For protection against harsh sun, consider installing awnings or planting shade trees.
Dealing with Water Damage Behind Insulated Siding
Water damage behind insulated siding is a serious issue that can lead to significant problems if left unaddressed. The trapped moisture can cause rot in the underlying wood framing, the growth of mold and mildew, and even structural damage to your home. Early detection and prompt action are key to minimizing the extent of the damage and preventing costly repairs down the line.
Identifying and Addressing Moisture Buildup
Moisture buildup behind insulated siding often manifests as discoloration or swelling of the siding itself. You might also notice water stains on interior walls or ceilings, a musty odor emanating from the affected area, or even the presence of visible mold or mildew. To confirm moisture problems, a moisture meter can be used to check the moisture content of the wall framing behind the siding. Higher-than-normal readings indicate the presence of trapped water.
Removing and Replacing Damaged Insulation
Once moisture is confirmed, the damaged insulation must be removed and replaced. This process typically involves carefully removing the affected siding panels to expose the insulation and underlying framing. Inspect the framing for rot or damage; any affected wood should be replaced. Then, install new, properly dried insulation, ensuring it’s adequately ventilated to prevent future moisture buildup. After replacing the insulation, reinstall the siding panels or replace them with new ones. Remember to wear appropriate personal protective equipment (PPE) such as gloves and eye protection throughout this process.
Improving Ventilation and Moisture Control
Preventing future water damage requires improving ventilation and moisture control. Properly functioning gutters and downspouts are crucial to divert water away from the foundation and siding. Consider installing a vapor barrier on the interior wall to prevent moisture migration from inside the house. Adequate attic ventilation helps prevent moisture buildup within the wall cavity. Regular inspections of your siding and gutters can also help catch problems early. For example, ensuring your gutters are cleaned at least twice a year can prevent water from overflowing and seeping behind your siding. A well-maintained home is less prone to such problems.
Visual Guide to Insulated Siding Repair
Understanding the visual cues of damage to your insulated siding is the first step towards effective repair. A quick visual inspection can save you time and money by allowing you to accurately assess the extent of the problem and choose the appropriate repair method. This guide will help you identify common types of damage and understand their causes.
Types of Insulated Siding Damage
Different types of damage to insulated siding present distinct visual characteristics. Recognizing these differences is crucial for selecting the right repair technique. Failing to do so could lead to further damage or an ineffective repair.
- Cracks: Thin, hairline cracks often appear as spiderweb-like patterns or single, straight lines. These are frequently caused by settling of the house foundation, thermal expansion and contraction, or impact damage from small objects. Larger cracks may indicate more serious structural issues. The cracks may be visible on the surface of the siding, or sometimes, you might only see a slight discoloration along the crack line.
- Holes: Holes range from small punctures caused by impacts (e.g., from a thrown object or a flying debris) to larger openings caused by more significant impacts or animal damage. The size and shape of the hole will vary greatly depending on the cause. You may see the underlying insulation material exposed through the hole.
- Discoloration: Uneven fading or discoloration, often appearing as streaks or patches, can indicate sun damage, water damage, or mildew growth. Sun damage usually occurs on the side of the house that receives the most direct sunlight, causing the color to fade unevenly. Water damage may manifest as darker streaks or blotches, especially near the bottom of the siding. Mildew often appears as a dark, fuzzy growth.
- Warping: Warped siding panels bulge or curve outward, often caused by moisture penetration or significant temperature fluctuations. The warping can be slight or quite pronounced, affecting the overall appearance and potentially compromising the siding’s structural integrity. Severe warping might involve buckling or separation of the panels.
Tools and Materials for Insulated Siding Repair
The tools and materials required for repairing insulated siding depend on the type and extent of the damage. Having the right tools on hand will make the repair process smoother and more efficient. Improper tools can lead to further damage to the siding or an unsatisfactory repair.
- Minor Repairs (Cracks, Small Holes): For minor repairs, you will typically need a putty knife, caulking gun, exterior-grade caulk (matching the siding color), and possibly a small brush for cleaning the area before applying caulk. Fine-grit sandpaper might be useful to smooth out rough edges before caulking.
- Moderate Repairs (Larger Holes, Moderate Warping): For larger holes or moderate warping, you may need additional materials like a replacement siding panel (matching the existing siding), a utility knife, measuring tape, screws, and a drill with appropriate drill bits. Depending on the location and extent of the damage, you might also need backing materials like wood or metal flashing to provide support behind the replacement panel.
- Major Repairs (Extensive Damage, Water Damage): Major repairs may require the expertise of a professional contractor. However, you will still need to gather information about the extent of the damage. This may involve removing some siding panels to assess the water damage. Safety equipment like gloves and eye protection is essential when working with potentially damaged siding.
Summary
Repairing your insulated siding doesn’t have to be daunting. By following these tips and taking preventative measures, you can extend the life of your siding and maintain your home’s value and beauty. Remember, early detection and prompt action are key to preventing minor issues from becoming major headaches. With a little knowledge and effort, you can keep your home looking its best for years to come.