Durable Insulated Siding Options: A Guide
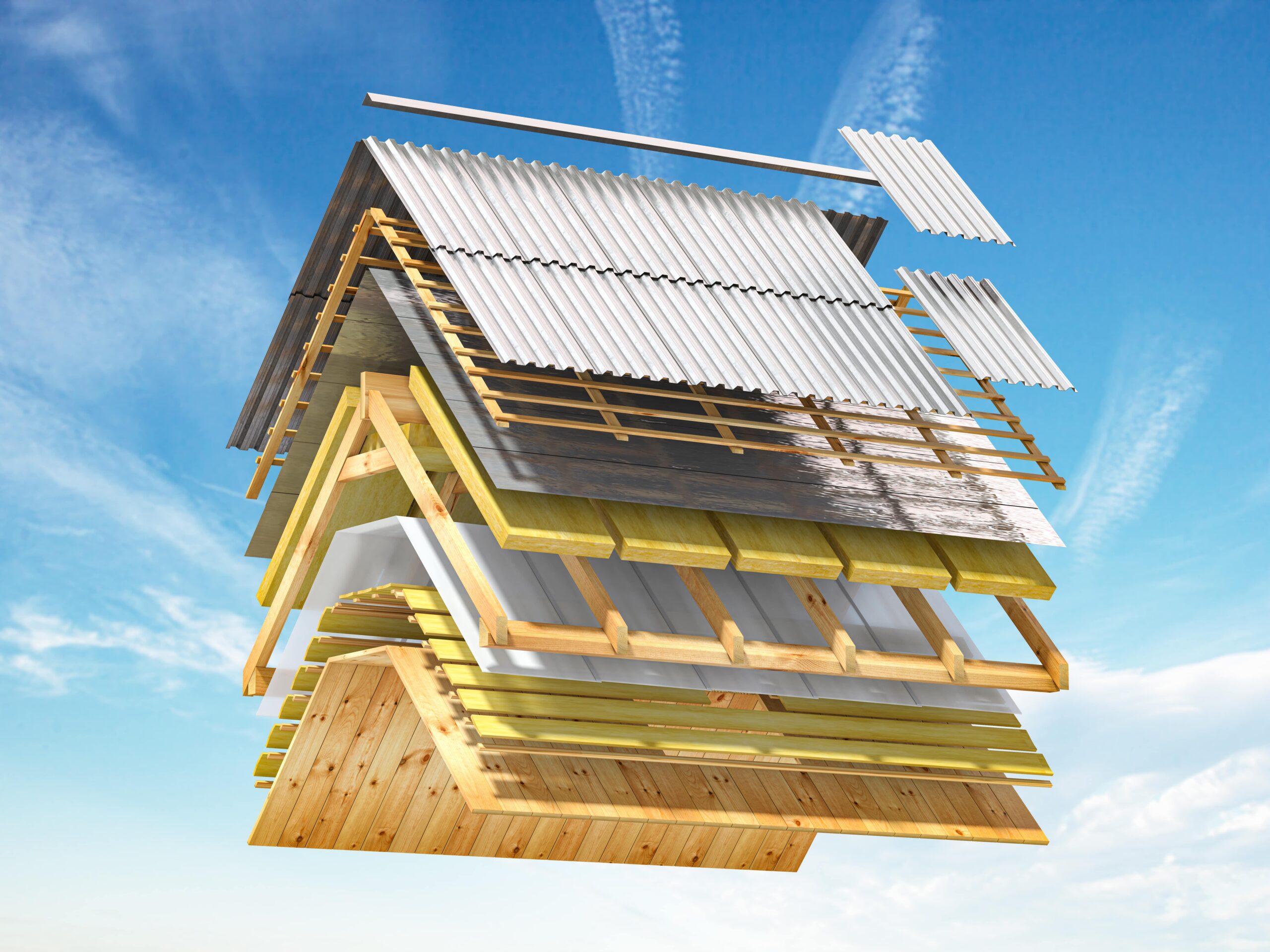
Durable insulated siding options offer a blend of beauty, energy efficiency, and longevity for your home. Choosing the right siding isn’t just about aesthetics; it’s about investing in a durable, energy-saving solution that protects your home for years to come. This guide explores the various materials, installation processes, and long-term considerations to help you make an informed decision.
From the initial cost analysis to the environmental impact, we’ll delve into the specifics of each siding type, comparing their pros and cons to assist you in finding the perfect fit for your home and budget. We’ll examine factors like R-value, lifespan, and maintenance requirements, empowering you to choose a siding option that aligns with your lifestyle and long-term goals.
Types of Durable Insulated Siding
Choosing the right insulated siding can significantly impact your home’s energy efficiency, curb appeal, and longevity. Understanding the different materials and their properties is key to making an informed decision. This section explores the characteristics of several popular and durable options.
Durable Insulated Siding Materials
Selecting the right siding material depends on various factors, including budget, aesthetic preferences, and climate. The following table summarizes the pros, cons, and typical lifespans of common durable insulated siding materials.
Material | Pros | Cons | Typical Lifespan (Years) |
---|---|---|---|
Fiber Cement | Durable, fire-resistant, low maintenance, paintable, can mimic wood textures | More expensive than vinyl, can be brittle, requires professional installation | 50-80 |
Vinyl | Affordable, low maintenance, variety of colors and styles, easy installation | Can fade or crack in extreme temperatures, less durable than fiber cement or metal, not as environmentally friendly as some other options | 20-40 |
Engineered Wood | Aesthetically pleasing, good insulator, relatively durable | Susceptible to moisture damage if not properly installed and maintained, more expensive than vinyl, requires regular maintenance including painting | 30-50 |
Metal (Aluminum or Steel) | Extremely durable, fire-resistant, low maintenance, long lifespan, energy efficient | Can dent, susceptible to scratches, higher initial cost, can be noisy in hail or rain | 50-75+ |
Manufacturing Processes and Durability
The manufacturing process significantly impacts a material’s durability. Fiber cement siding is created by mixing cement, cellulose fibers, and other additives, then formed under pressure and cured. This process results in a strong, rigid panel resistant to fire, insects, and rot. Vinyl siding is extruded from polyvinyl chloride (PVC) resin, a process that creates a relatively flexible yet durable material. Engineered wood siding often involves treating wood fibers with resins and adhesives, creating a composite that’s more resistant to moisture and decay than solid wood. Metal siding is manufactured from sheets of aluminum or steel, often coated with a protective layer to enhance durability and prevent corrosion. These coatings can include paint, powder coatings, or other specialized finishes.
Thermal Performance of Insulated Siding
Insulated siding’s primary benefit lies in its improved thermal performance. This is quantified using the R-value, which represents the material’s resistance to heat flow. Higher R-values indicate better insulation. While precise R-values vary depending on the specific product and thickness, generally, fiber cement siding offers a moderate R-value, vinyl siding has a relatively low R-value, engineered wood offers a better R-value than vinyl but less than fiber cement, and metal siding, especially with added insulation backing, can achieve high R-values. The R-value is often combined with the insulation behind the siding to calculate the overall thermal resistance of a wall system. For example, a wall with 6 inches of fiberglass insulation (R-19) behind metal siding with an R-value of 4 will have a total R-value of approximately R-23. This demonstrates how siding contributes to, but doesn’t solely determine, the overall wall insulation performance.
Installation Methods and Best Practices
Installing insulated siding is a significant home improvement project that enhances both the aesthetics and energy efficiency of your home. Proper installation is crucial for longevity and performance. Understanding the process and adhering to best practices will ensure a successful and lasting result.
Different insulated siding types require slightly different installation methods. We will explore two common types: foam-backed vinyl siding and fiber cement insulated siding. Both require careful preparation of the wall surface for optimal results.
Foam-Backed Vinyl Siding Installation
Foam-backed vinyl siding offers a relatively straightforward installation process. However, precision and attention to detail are key to achieving a professional finish. Proper preparation of the underlying wall is paramount to prevent future problems.
- Surface Preparation: Begin by thoroughly cleaning the wall surface, removing any loose paint, debris, or old siding. Repair any damaged areas of the underlying sheathing or wall. Ensure the wall is dry and free of moisture. This step is crucial for preventing moisture buildup behind the new siding, which can lead to mold and rot.
- Starter Strip Installation: Install a starter strip along the bottom edge of the wall, ensuring it’s level and plumb. This provides a consistent starting point for the siding panels.
- Siding Panel Installation: Begin installing siding panels from the bottom, working your way up. Each panel should be overlapped and fastened securely using the appropriate nails or screws, ensuring proper spacing and alignment. Follow the manufacturer’s instructions regarding nail placement and spacing to prevent warping or damage.
- J-Channel and Corner Trim: Use J-channel and corner trim to finish the edges and corners neatly. These elements provide a clean, professional look and protect the edges of the siding panels from damage.
- Finishing Touches: Install any necessary accessories such as window and door trim to complete the installation. Inspect the finished installation carefully to ensure all panels are properly aligned and fastened.
Fiber Cement Insulated Siding Installation
Fiber cement insulated siding offers superior durability and fire resistance compared to vinyl. Its installation, however, requires more precision and often specialized tools.
- Surface Preparation: As with vinyl siding, thorough cleaning and repair of the wall surface are essential. Pay close attention to any areas of moisture penetration or damage, addressing them before installation. A properly prepared surface is the foundation of a successful installation.
- Framing and Sheathing: Fiber cement siding often requires a more robust underlying structure. Ensure the wall framing is sound and the sheathing is properly installed and secured. This provides a stable base for the siding panels.
- Siding Panel Installation: Fiber cement panels are typically larger and heavier than vinyl, requiring careful handling and precise placement. Use appropriate fasteners, spacing, and techniques as recommended by the manufacturer. Consider using a level and plumb bob to ensure accurate alignment.
- Caulking and Sealing: Proper caulking and sealing are critical with fiber cement to prevent moisture penetration. Apply caulk to all seams and joints to create a watertight barrier. This is essential for the longevity and performance of the siding.
- Finishing Touches: Install trim, flashing, and other accessories as needed, paying close attention to detail to ensure a professional and watertight installation.
Proper Fastening Techniques
The method of fastening siding varies depending on the material. Proper fastening is critical for preventing damage and ensuring a long-lasting installation. Incorrect fastening can lead to warping, cracking, or even failure of the siding.
Imagine a visual representation: For vinyl siding, picture small nails spaced evenly along the top edge of each panel, slightly below the overlapping panel above. For fiber cement, visualize larger, corrosion-resistant screws driven into the panel at designated locations, ensuring they are deeply seated but not over-tightened to avoid cracking.
Wall Surface Preparation Best Practices
Preparing the wall surface before siding installation is crucial for a successful and long-lasting result. Proper moisture management and insulation techniques are key elements of this preparation.
Before installing any siding, thoroughly inspect the wall for any signs of moisture damage, such as rot, mildew, or water stains. Address any issues promptly, including repairing or replacing damaged sections of the wall. Ensure the wall is completely dry before proceeding with the installation. Proper insulation will also help prevent moisture buildup and improve the energy efficiency of your home. Consider adding additional insulation where necessary to meet current building codes and energy efficiency standards.
Maintenance and Lifespan Considerations
Protecting your investment in insulated siding requires a proactive approach to maintenance. Regular care not only enhances the appearance of your home but also significantly extends the lifespan of your siding, saving you money and hassle in the long run. Understanding the specific needs of your siding material is key to ensuring its longevity.
Regular maintenance prevents small problems from escalating into costly repairs. A little effort now can save significant expense and disruption later. This section details a routine maintenance schedule and addresses common issues for various insulated siding types.
Routine Maintenance Schedule
A consistent maintenance plan is crucial for all insulated siding types. This involves regular cleaning, inspections for damage, and prompt repairs. For example, a homeowner might schedule a spring cleaning and a fall inspection, adjusting the frequency based on their climate and siding material.
- Cleaning: Most insulated siding can be cleaned with a garden hose and a soft-bristled brush. For tougher stains, a mild detergent solution can be used, followed by thorough rinsing. Avoid high-pressure washers, as they can damage the siding. For vinyl siding, a simple solution of water and mild dish soap is usually sufficient. For fiber cement, a pressure washer (low-pressure setting) can be used, but caution is needed to avoid damage.
- Inspection: Regularly inspect your siding for signs of damage, such as cracks, loose panels, or insect infestation. Pay close attention to areas prone to moisture buildup, like around windows and doors. Early detection of problems allows for timely repairs, preventing further damage.
- Repair: Promptly address any damage to prevent it from worsening. Minor repairs, like replacing a damaged panel, can often be done by a homeowner with basic DIY skills. More extensive repairs should be handled by a professional contractor.
Common Issues and Solutions
Different insulated siding materials are susceptible to various problems. Understanding these issues and their solutions is essential for effective maintenance.
- Vinyl Siding: Common problems include cracking, warping, and fading. Cracking can be caused by impact or extreme temperature changes. Warping may result from improper installation or exposure to excessive heat. Fading is often due to prolonged sun exposure. Solutions involve replacing damaged panels and using appropriate cleaning methods.
- Fiber Cement Siding: Fiber cement siding is durable but can be susceptible to cracking and moisture damage if not properly sealed. Cracking can be caused by impact or settling of the house. Moisture damage can lead to mold and mildew growth. Solutions involve prompt repair of cracks and ensuring proper sealing around windows and doors.
- Insulated Metal Siding: Metal siding is very durable but can be susceptible to dents and scratches. It can also be prone to rusting if the protective coating is damaged. Solutions involve careful handling during maintenance and prompt repair of any damage to the protective coating.
Factors Influencing Lifespan
Several factors influence the lifespan of insulated siding. Addressing these factors during the initial selection and installation process can significantly extend the life of your siding.
- Climate: Extreme temperature fluctuations and harsh weather conditions, such as heavy snow or strong winds, can shorten the lifespan of siding. Homes in areas with severe weather conditions may require more frequent maintenance.
- Installation Quality: Proper installation is crucial for the longevity of insulated siding. Improper installation can lead to issues such as water damage, cracking, and premature failure.
- Material Selection: The choice of siding material significantly impacts its lifespan. Some materials, such as fiber cement, are naturally more durable than others, like vinyl.
- Maintenance Practices: Regular maintenance, including cleaning, inspection, and timely repairs, significantly extends the life of insulated siding. Neglecting maintenance can lead to premature deterioration and costly repairs.
Cost Analysis and Value Proposition
Choosing insulated siding involves a careful consideration of upfront costs and long-term savings. While the initial investment might seem significant, the energy efficiency and durability of insulated siding often translate to substantial long-term value. This section analyzes the cost factors and demonstrates the return on investment.
The total cost of insulated siding installation varies significantly based on several factors, including the type of siding chosen, the size of the house, the complexity of the installation, and regional labor rates. It’s crucial to obtain multiple quotes from reputable contractors to compare pricing and understand the scope of work included.
Insulated Siding Cost Comparison
The table below provides a general comparison of the initial costs for different types of insulated siding. Remember that these are estimates, and actual costs can vary widely depending on the factors mentioned above. It is crucial to consult with local contractors for accurate pricing in your area.
Material | Material Cost (per sq ft) | Labor Cost (per sq ft) | Total Cost (per sq ft) |
---|---|---|---|
Fiber Cement | $3.00 – $6.00 | $2.00 – $4.00 | $5.00 – $10.00 |
Vinyl (Insulated) | $2.00 – $4.00 | $1.50 – $3.00 | $3.50 – $7.00 |
Metal (Insulated) | $4.00 – $8.00 | $2.50 – $5.00 | $6.50 – $13.00 |
Polyurethane Foam | $5.00 – $10.00 | $3.00 – $6.00 | $8.00 – $16.00 |
Long-Term Cost Savings and Energy Efficiency
The energy efficiency benefits of insulated siding significantly impact the overall value proposition. By reducing heat transfer, insulated siding lowers heating and cooling costs. This translates to substantial long-term savings, potentially offsetting the higher initial investment within a few years. For example, a homeowner in a climate with significant temperature fluctuations might save hundreds or even thousands of dollars annually on energy bills. This savings is directly related to the R-value of the siding; higher R-values generally indicate better insulation and greater energy savings.
Return on Investment (ROI)
The ROI for insulated siding varies depending on several factors, including the initial cost, energy savings, siding lifespan, and maintenance costs. Generally, insulated siding offers a positive ROI over its lifespan. For instance, a homeowner investing in higher-priced, more energy-efficient siding might experience a faster return on their investment compared to someone opting for a less expensive option with lower energy savings. A detailed ROI calculation should consider the projected energy savings over the siding’s expected lifespan (typically 20-50 years), factoring in potential increases in energy prices. This analysis helps determine the payback period – the time it takes for the energy savings to equal the initial investment. A shorter payback period indicates a stronger ROI.
Environmental Impact and Sustainability
Choosing sustainable building materials is crucial for minimizing our environmental footprint. Insulated siding, while offering numerous benefits, carries an environmental impact throughout its lifecycle, from manufacturing to disposal. Understanding this impact allows for informed decisions that prioritize both building performance and environmental responsibility. This section analyzes the environmental implications of various insulated siding materials and explores the role of sustainable practices in mitigating these impacts.
Manufacturing and Disposal Impacts of Insulated Siding Materials
The environmental impact of insulated siding varies significantly depending on the materials used. Consideration should be given to the energy consumption during manufacturing, transportation, and the potential for pollution during these processes, as well as the ease and environmental impact of disposal at the end of the siding’s lifespan.
- Vinyl Siding: Vinyl siding production is energy-intensive, relying heavily on fossil fuels. Disposal often involves landfill space, contributing to waste accumulation. Some vinyl siding contains PVC, a material known for its persistent presence in the environment and potential negative impacts on ecosystems.
- Fiber Cement Siding: Fiber cement siding manufacturing uses cement, which has a high carbon footprint due to the energy required for its production and transportation. However, fiber cement is a durable material with a longer lifespan, potentially offsetting some of the initial environmental impact. Disposal may require special handling due to the presence of cement and other components.
- Wood Siding: While wood is a renewable resource, the environmental impact of wood siding depends heavily on the sourcing practices. Sustainably harvested wood from responsibly managed forests minimizes environmental damage. However, untreated wood is susceptible to rot and insect damage, requiring more frequent replacement and potentially increasing its overall environmental impact. Disposal can be more environmentally friendly compared to vinyl or fiber cement, as wood is biodegradable.
- Metal Siding: Metal siding, such as aluminum or steel, requires significant energy input during its manufacturing. However, metal is highly recyclable, reducing the environmental impact at the end of its life. The environmental impact also depends heavily on the sourcing of the raw materials and the energy efficiency of the manufacturing process.
Recycled Content and Sustainable Manufacturing Practices
Increasingly, manufacturers are incorporating recycled content into insulated siding and adopting sustainable manufacturing practices to reduce the environmental footprint of their products.
The use of recycled materials, such as post-consumer recycled plastic in vinyl siding or recycled aluminum in metal siding, decreases the demand for virgin materials and reduces landfill waste. Sustainable manufacturing practices include minimizing energy consumption, reducing water usage, and implementing waste reduction strategies throughout the production process. Certifications like LEED (Leadership in Energy and Environmental Design) can help identify products manufactured with environmentally conscious practices.
Energy Efficiency and Overall Building Sustainability
Insulated siding plays a significant role in a building’s overall energy efficiency and sustainability. Its ability to reduce heat transfer contributes directly to lower energy consumption for heating and cooling.
High-performance insulated siding options can significantly reduce a building’s energy needs, leading to lower greenhouse gas emissions and reduced reliance on fossil fuels. The energy savings generated over the siding’s lifespan can offset some of the environmental impacts associated with its manufacturing and disposal. For example, a home with high-performance insulated siding might see a 15-20% reduction in heating and cooling costs compared to a home with less efficient siding, leading to substantial long-term environmental benefits.
Conclusive Thoughts
Ultimately, selecting durable insulated siding is a significant investment that impacts both the aesthetic appeal and the energy efficiency of your home. By carefully considering the factors discussed—material properties, installation techniques, maintenance needs, and long-term costs—you can make a confident choice that enhances your home’s value and comfort for many years. Remember to consult with professionals for personalized advice tailored to your specific needs and climate.